Epson gyroscope sensors XV7000 series suitable for AGV logistics robots: XV7001BB, XV7011BB. Previously, we all knew that XV7001BB and XV7011BB were suitable for sweeping robots. In fact, for AGV logistics robots, the XV7000 series gyroscope sensor is also an important part of it. AGV robots, also known as AGV handling robots or AGV carts. With the rapid development of information technologies such as the Internet of Things, big data, and mobile applications, "robot replacement" is gradually being implemented in the manufacturing industry. AGV robots are playing a crucial role in material handling, flexible, and automated production in the manufacturing industry. AGV robots not only achieve unmanned material handling operations, but also require a large amount of information collection to be transmitted to the entire Internet of Things through AGV intelligent terminals. AGV wheeled automatic navigation robots are one of the more mature industrial robots in China. Many AGV automatic navigation robots are basically composed of guidance modules, walking modules, guidance sensors, microprocessors, communication devices, solar cells, etc. Among them, directional sensors are the foundation of modern AGVs. Without human intervention, all actions of AGV come from the perception of external objects by the gyroscope sensor. Therefore, sensor technology is a crucial part of AGV technology.
The AGV robot obstacle prevention system adopts non-contact laser anti-collision sensors to protect it from collision damage during operation and ensure safe operation. When an obstacle is detected, it can automatically slow down and stop, and after the obstacle disappears, it can automatically resume operation. Under the action of sensors, AGV robots can not only ensure the safety of the system, surrounding operators, and equipment in various situations, but also effectively ensure the safety of system operation and improve system efficiency. Based on different guidance sensors, AGV guidance methods can be divided into many types, such as inertial guidance, laser guidance, magnetic guidance, and ultrasonic guidance. In the guidance method of AGV logistics robots, there is a fixed route guidance method that uses magnetic sensors and gyroscopes. Its working principle is to use a specially designed Fenger position sensor to detect small magnets installed on the ground, and then use gyroscope technology to continuously control the direction of AGV operation. Gyroscope is a solid-state angular rate sensor, whose output voltage is proportional to the speed on its sensitive axis to determine the direction of AGV operation. It is understood that if high-quality sensor components are used, the magnet+gyroscope guidance system has high accuracy, some can reach up to+3 millimeters. Meanwhile, using standard components can significantly reduce costs, which are much lower than electromagnetic induction guided methods. Therefore, this guidance method is suitable for situations where guide cables cannot be buried.
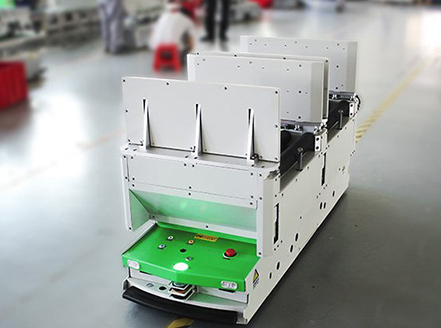
It has to be mentioned here that Ai Jinsheng's anti glare sensor XV7000 series:
The single axis digital 12C interface output sensor of XV7011BB is different from the silicon material used in anti screw instruments using MEMS technology. XV7011BB uses quartz material. When the product rotates, XV7011BB detects angular velocity by applying Coriolis force to the vibrating element, greatly improving the deviation and achieving stable temperature characteristics of angular velocity output in a stationary state. In AGV logistics robots, the excellent temperature drift characteristics of the gyroscope XV7011BB help AGV logistics robots achieve more accurate path planning and actual operation. Engineers measure the angle changes of the AGV vehicle's movement using an anti sway device, and control the forward direction of the AGV robot. XV7011BB can effectively solve the path planning problem of the AGV logistics robot. In terms of gyroscope sensors, EPSON's digital output anti sway device XV7001BB is made of crystal material and has good drift characteristics, with a deviation of only+1/, resulting in more accurate path planning and actual operation. The EPSON sensor XV7001BB adopts a highly integrated circuit design to ensure more reliable quality of AGV logistics robot products.