With the increasing speed of global warming, natural disasters such as sudden rainstorm and flood have become frequent in the world today. Faced with such a challenge, data monitoring of machine operation status to correctly operate gates and dams to control waterways is essential for community safety. Under the threat of the Sword of Damocles, EPSON launched the M-A342 series three-axis vibration sensors with M-A342 and M-A342VD10 as its core to optimize data monitoring.
According to the commonly used 3S (sensing system, decision system, and control system) architecture, the first step in machine health detection is sensor signal acquisition, with vibration signal monitoring being one of the most commonly used monitoring parameters. By measuring the vibration of motors that open and close gates and dams in accordance with ISO standards, Epson's vibration sensors enable infrastructure operators to evaluate the condition of equipment and perform maintenance as needed. Epson hopes that its vibration sensors can play a role in protecting social infrastructure, which is crucial for ensuring community safety.
EPSON's three-axis vibration sensor M-A342 series adopts advanced quartz processing technology, which has the characteristics of low sound and high stability, and can achieve accurate measurement of vibration speed. The low inter axis sensitivity and low error ensure high accuracy of the measured data, which is crucial for vibration monitoring as it directly relates to the accurate judgment of equipment health status. The sensor has a built-in self check function, which can effectively improve product stability by calling the corresponding registers to obtain the diagnostic results of the sensor. Due to the use of Epson's unique microfabrication technology, crystal vibration sensor components have the characteristics of low noise, high stability, and low power consumption.
Ordinary sensors generally have monitoring defects and maintenance issues. Taking the vibration signal detection of machine tools as an example, the impact and background vibration during the machining process may submerge weak vibration signals, making it difficult to accurately measure the small vibrations of tools or workpieces. However, these weak signals often have important value in monitoring tool wear and determining the quality of workpiece processing; During the cutting process, there are both high and low frequency vibrations. If the sensor cannot cover a sufficiently wide frequency range, it may lead to important vibration information being missed, thereby affecting machining accuracy and product quality.
Epson's three-axis vibration sensor M-A342 series, with its excellent technical parameters, provides a solid guarantee for lathe vibration monitoring, ensuring the accuracy and reliability of work. An example of machine tool vibration signal detection is the M-A342 series three-axis vibration sensor, which covers a vibration speed range of+100 mm/s at frequencies ranging from 1Hz to 1000 Hz. It can capture various vibrations from low frequency to high frequency, meeting the detection requirements of ISO 20816 standard for the vibration speed of general CNC machine tool spindle motors, ensuring comprehensive monitoring of the vibration speed of CNC machine tool spindle motors, ensuring the monitoring coverage of the entire machining process, and solving the problem of insufficient support frequency bands that may occur during the cutting process; Meanwhile, its general speed detection sensitivity is 2.38 x10 ^ -4 (mm/s)/LSB, which means that even the smallest speed changes can be accurately captured.
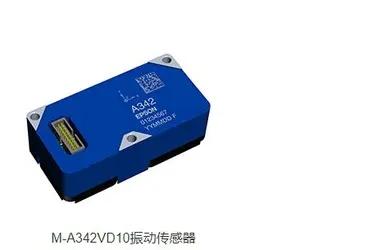
Not only that, the M-A342 series also has other advantages that comply with ISO 10816 and IS0 20816 standards: supporting speed and displacement output with a wide dynamic range: no need to adjust the measurement range to match the size of vibration, unaffected by magnetic fields: quartz crystal sensors can accurately measure motors that generate strong magnetic fields,
Anti noise: Digital output can resist the influence of noise
Simple measurement environment: No need for charging amplifiers, A/D converters, or other peripheral devices
High reliability: ensures an average time between failures (MTBF) of 87600 hours
These capabilities make the M-A342 series of three-axis vibration sensors very suitable for health monitoring of various machines, including but not limited to monitoring equipment such as machine tools, pumps, fans, and motors in the manufacturing industry. Accurate and reliable vibration analysis can predict equipment failures, thereby achieving preventive maintenance, reducing unexpected downtime, extending equipment lifespan, and ensuring production efficiency and quality.